Really quickly, I wanted to go through some news:
*Kezurou-kai USA is having its annual national event in Kingston, NY this weekend. I can’t make it, because I am headed back to Mount Fuji Wood Culture Society for a sashimono focused artist in residency next week. We are giving away 2 tickets that my brother and I can't use because of the Japan trip. Ideally the tickets go to a young carpenter who is interested in elevating their work through Japanese wood craft and tools, and who can't really afford the tickets to the event. Email me if you're interested. hello@paklan.org
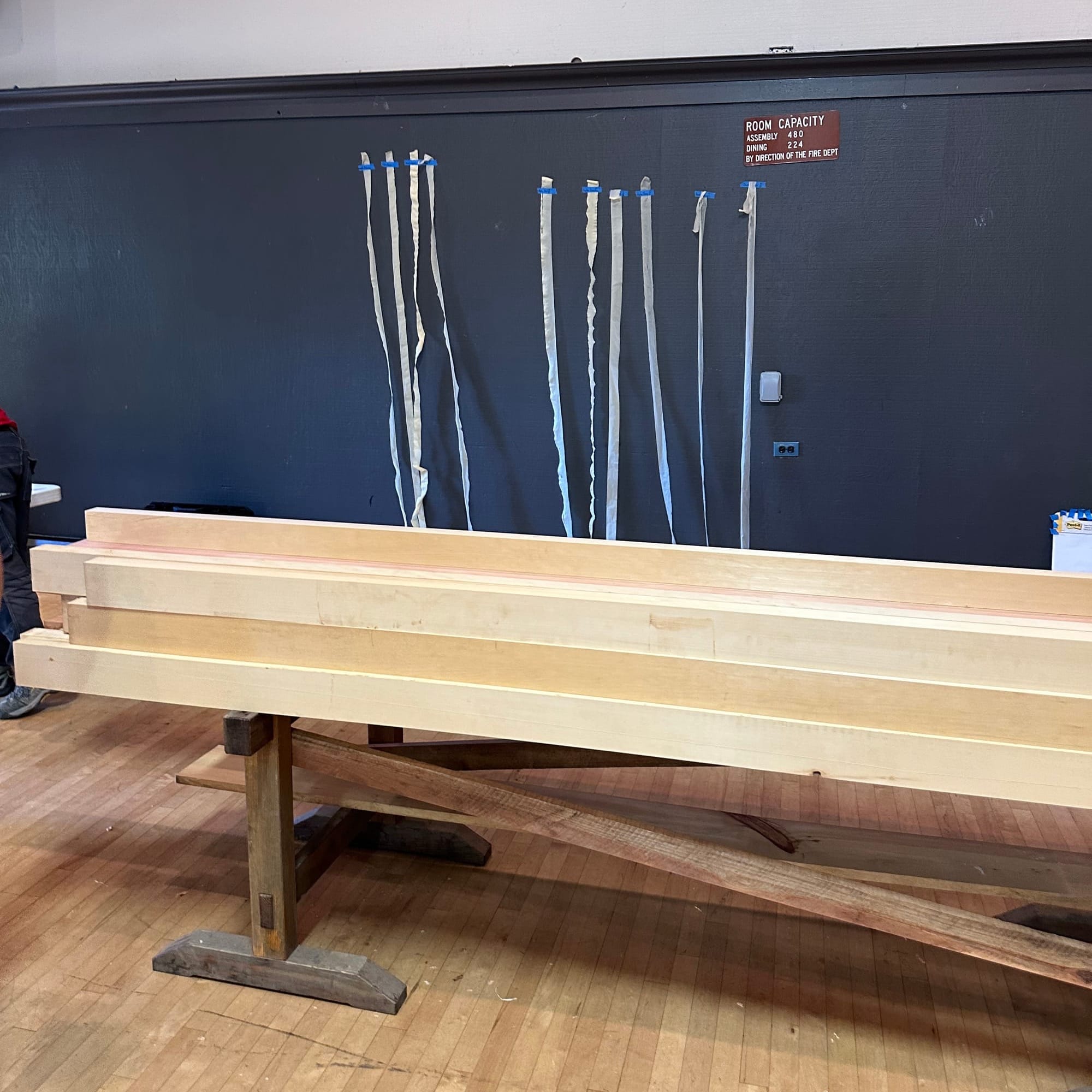
There’s been an intense amount of travel in a short amount of time. Last week, I went to visit Mokuchi to brush up on some joinery with Yann and catch up about work. I’ve taken this class twice before, once with him at the start of my journey and once last year with Dale. But there is no limit to the level of refinement in the most simple joints and chances to use them are not as often as you'd imagine without framing projects on hand. One idea he dropped on me last week that has my mind running circles is the idea that a tool can be too sharp. More on this as I get more reporting done on the concept.
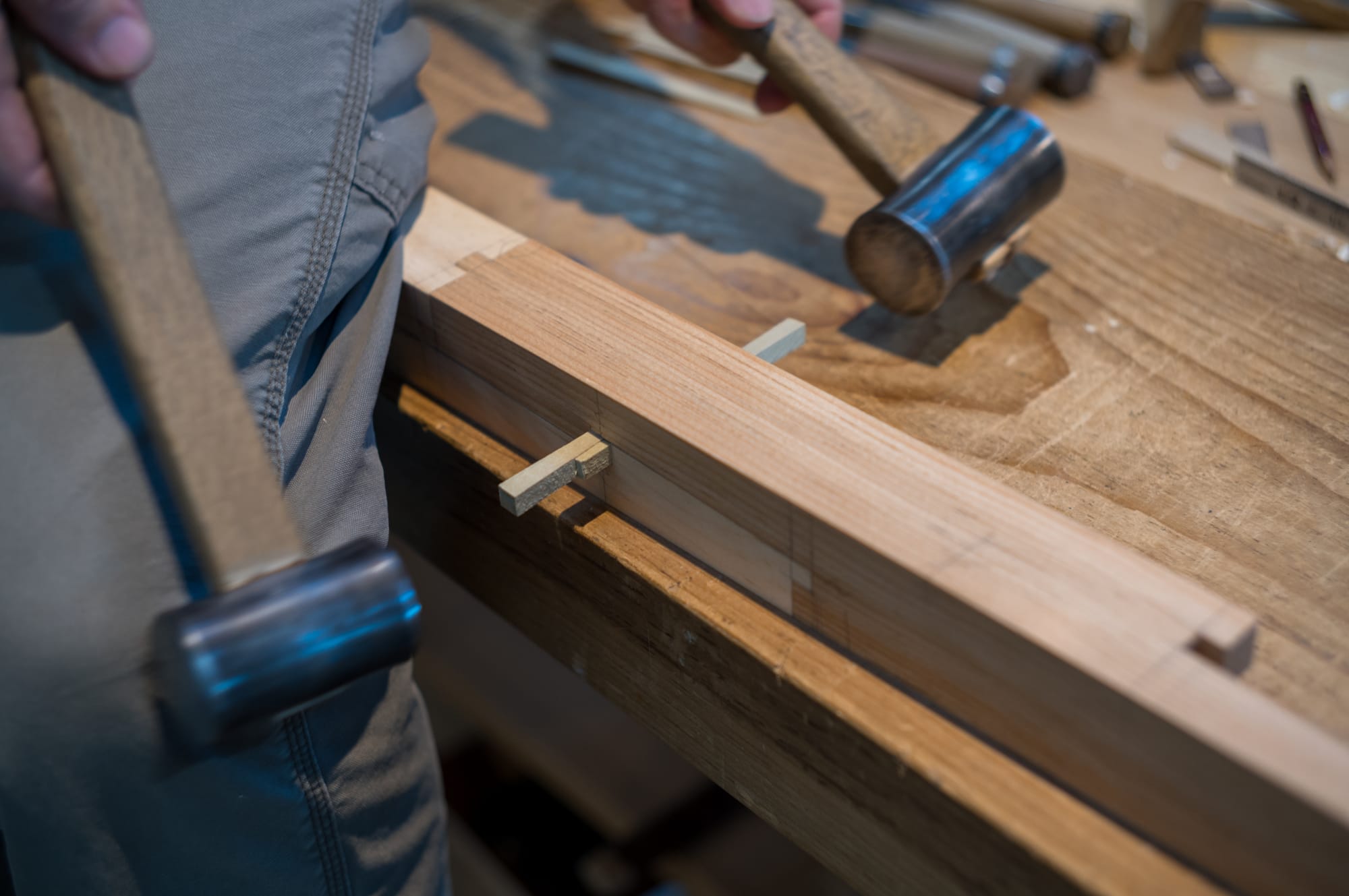
This week I figured I’d drop in a bit of tool talk for Japanese plane users who are curious about larger planes. Of course, I no longer review objects for a living, but those grooves in my neurology run deep, so I always have an outsized curiosity for tools.
Carpentry scale projects highlight a weakness in my isolated place in the islands, but also how I work these days. Carpentry is meant for teams and machine support, and it is always humbling in this regard for someone overly self-sufficient to realize the limits of a single person working in architectural scales. After a week of milling and planing–and then re planing–the Port Orford cedar walkway by hand, I essentially collapsed. Too abrupt of a rest, combined with floor sitting resulted in my entire right side tightening and twisting up. Planing is an asymmetric motion, pulling with the right legs, hips, back, arm and hand. And without work to temper those muscles, no amount of stretching would help. I feel my age during projects like this and recovery takes much longer than I would like to admit.
The walkway started checking without finish and with end grain exposed, giving me a better understanding of the utility of face boards usually shown in structures built like this, and western decks and their long grain exposures. Some Anchorseal on the ends fixed the problem and I'm most likely going to leave the boards unfinished as it is already aging very gracefully and resisting dirt and weather just fine. The epoxy pond coating was reapplied successfully by the masons and we are set to bring the koi home from a neighbor's house where they have been for 5 years before the holidays.

I generally cap a project with some shop maintence or tool setup. It’s a productive form of procrastination before approaching the next build.
It didn’t help the back problems that I chose to set up a slightly larger than-average new plane. The tool I decided to focus on was 3-sun in size in the shaku measurement system. Or about 90mm or a little over 3-½ inches wide. Compared to the standard smoothing plane of 70mm, it was just a little bit bigger and a far cry from the much larger planes we see at contests and demonstrations. I didn’t think it would be much more challenging to set up than a normal plane. But the slightly heavier body and blade made tuning more than proportionally more tricky.
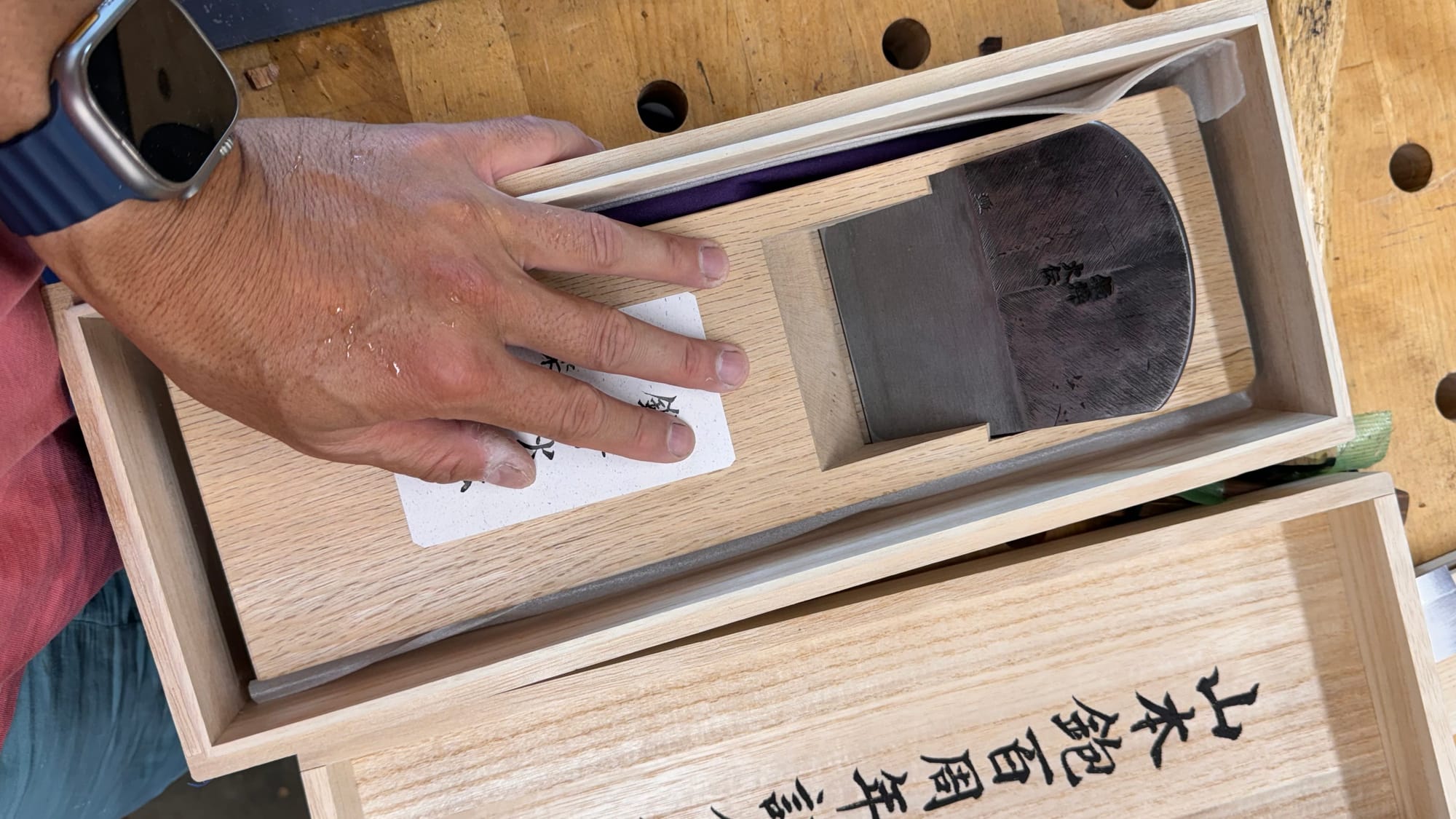
Planes like this are rare. There must be a reason for that, and I wondered how professionals use them in common work. The simple answer is that they aren’t needed for most pros and almost all hobbyists. And they aren’t necessarily worth the trouble in most cases. But not all.
The Sukiya style carpenters I study with sometimes–Yann Giguere and Dale Brotherton–had different examples of use. Yann said he had a few planes that are larger size, in the 80 to 110mm range. “They are fun and still manageable.” Andrew Ren, my friend and tool dealer, agreed that 90mm and below could be treated the same as standard size 70mm planes and cost only a little more when making custom orders.
After watching a 180mm plane demonstration at Kezuroukai USA, years ago, Dale said he thought to pick one up for the same purpose. He cut a dai, and was surprised at how much deflection a large blade and body could cause each other. It took him a month of evenings to tune up the plane for use.
I had heard of people using larger planes on Larry Ellison’s Japanese timber frame compound in the Bay Area, but some seniors on that project indicated planes might have been a little bit bigger. But, more significant members of the structures were planed with a super-surfacer.
I can’t remember where I heard this, but supposedly larger plane use was more common in Kansai region versus Kanto. This makes sense to me in terms of the variations of things like tatami mat and other architectural scales used between the east and the west as well as small differences in things like chisel handles. Eastern scale seems to have been smaller, overall, according to references like Engel’s The Japanese House.
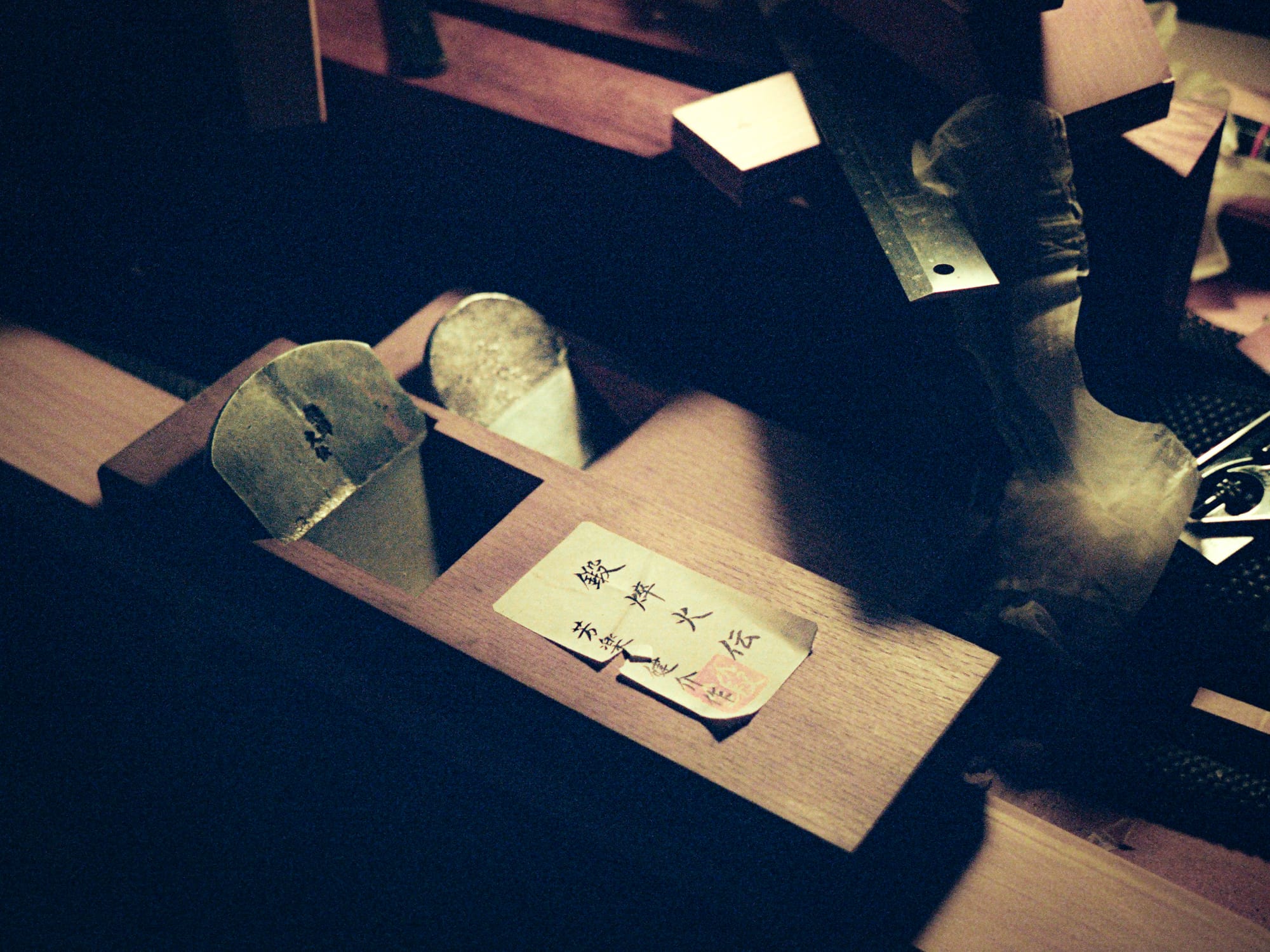
Jon Billing, told me one Kansai carpenter used his 90mm plane so little he turned it into a katsuo boshi, or plane for making bonito shavings.
When I spoke to Kohei Yamamoto of Somakosha, another teacher, he said that he had just used a 105mm plane on a tea room he was working on. Planing the posts in a single pass was ideal for eliminating the risk of track marks on the surface, he explained.
The tool’s size in proportion to the piece it is planing is one factor, another is its relation to a carpenter’s hand, and how easy it is to use and sharpen. Also in consideration is its width of cut, how thin of a cut it needs to take to be manageable, and how tolerant that longer straight edge is of surface irregularities. And how tolerant the wooden body is of weather changes.
A graceful balance between all these factors is found in the popular average-sized 70mm plane. A slightly larger human might opt for larger planes, but a smaller human might want the opposite. Those who work on larger and smaller bodies of work might shift their preferences appropriately, but in the end, human scale dictates the size of the work and what can fit in our hands.
Since this topic has never been written about in english, I thought to include some minor advice and context that might help someone interested in using slightly larger planes: